Highlights:
- The manufacturing industry has always been driven by innovation, constantly seeking ways to optimize processes, minimize costs, and deliver top-notch products.
- Enter cloud-based digital twin technology, a cutting-edge solution that enables manufacturers to bridge the gap between the physical and virtual worlds.
- By leveraging cloud-based digital twin technology, manufacturers can simulate, optimize, and predict with greater efficiency and accuracy.
- When it comes to making a substantial impact in this field, one company stands out: Microsoft. By bringing innovation to the forefront of manufacturing, Microsoft Azure is playing a vital role in accelerating the implementation of Cloud-based Digital Twin Technology.
In this Blog
Picture this: creating virtual replicas of physical assets and processes to unlock simulation, optimization, and predictive modeling. Sounds intriguing, right? This is real, and it’s transforming how manufacturers operate, making them more efficient and enhancing the quality of their products. So, fasten your seatbelts as we embark on this captivating exploration of cloud-based digital twin technology and its game-changing potential.
The manufacturing industry has always been driven by innovation, constantly seeking ways to optimize processes, minimize costs, and deliver top-notch products. Traditional manufacturing methods rely heavily on physical prototypes and trial-and-error approaches, which can be time-consuming, expensive, and prone to errors. Enter cloud-based digital twin technology, a cutting-edge solution that enables manufacturers to bridge the gap between the physical and virtual worlds. At its core, digital twin technology involves creating virtual replicas of real-world objects, systems, or processes. It’s like having a clone or a doppelgänger of a physical asset but in the digital realm. These digital twins capture and mirror the behavior, characteristics, and performance of their physical counterparts. What sets cloud-based digital twins apart is the utilization of the cloud infrastructure to host and manage these virtual replicas.
Understanding Cloud-Based Digital Twin Technology
Before we delve into the digital twin aspect, let’s understand the importance of cloud computing in manufacturing.
Cloud computing provides a scalable and flexible infrastructure for implementing digital twins. It offers advantages such as cost savings, accessibility, and powerful computing capabilities. In fact, Statista predicts that the global cloud computing market will reach a staggering $623.3 billion by 2023, signifying its growing significance in various industries.
One of the primary advantages of cloud computing is cost efficiency. Manufacturers no longer need to invest in expensive on-premises infrastructure and maintenance. Instead, they can rely on cloud service providers who offer pay-as-you-go models, allowing businesses to scale their computing resources based on their needs. This flexibility eliminates the need for upfront capital investment and enables manufacturers to allocate resources more efficiently.
Now, let’s introduce Cloud-Based Digital Twin Technology to the manufacturing scene. According to Gartner, by 2023, 30% of all manufacturers will use digital twins, resulting in a 10% improvement in effectiveness. Notably, the manufacturing industry stands as the primary adopter of digital twin solutions, commanding over 50% of the market share.
Digital twins serve as virtual replicas of real-world objects or systems, bridging the gap between physical and virtual realms. Manufacturers leverage these replicas to gain insights, perform analyses, and make informed decisions. Envision a future where cloud-based digital twins interconnect across industries, forming a vast network mirroring the physical world. They exchange data, learn from one another, and autonomously optimize operations. Such an ecosystem extends beyond individual manufacturing processes, encompassing supply chains, transportation systems, smart cities, and more.
In this scenario, the boundaries between physical and virtual blur. Active participants in decision-making, digital twins respond to real-time data and autonomously adjust processes for maximum efficiency, waste reduction, and environmental sustainability. They fuel innovation, fostering collaboration and knowledge sharing across industries, governments, and communities.
As digital twins evolve, they surpass mere replicas, developing intelligence by leveraging advanced technologies such as AI, machine learning, and predictive analytics. They anticipate future scenarios, optimize outcomes, and become proactive entities that revolutionize maintenance concepts.
This interconnected network also unlocks opportunities for sustainable practices. Real-time data on resource consumption, energy efficiency, and environmental impact empowers decision-makers to make informed choices and drive sustainability initiatives. Optimized supply chains reduce waste and carbon footprint, while efficient energy management minimizes resource consumption and greenhouse gas emissions.
Nevertheless, with the power of interconnected digital twins come challenges and ethical considerations. Privacy and security concerns arise due to the sharing and analysis of vast amounts of sensitive data. Striking a balance between data-driven optimization and human judgment becomes paramount. We must contemplate the extent of control we are willing to relinquish to autonomous digital twins and establish safeguards for transparency, accountability, and ethical decision-making.
In this compelling future, cloud-based digital twins in manufacturing offer benefits that go beyond individual processes. This groundbreaking technology is not just a passing trend; it is projected to reach a staggering $48.2 billion market value by 2026. With a remarkable compound annual growth rate (CAGR) of 20%, it stands as the fastest-growing segment in the industry. It will revolutionize every aspect of design, production, and operations, propelling us into an era of unprecedented innovation, sustainability, and collaboration on a global scale. As we embrace this transformative technology, we push the boundaries of what is achievable and challenge ourselves to navigate the complexities of an interconnected digital world while remaining steadfast to our core values and aspirations.
7 Key Components of Cloud-Based Digital Twin Technology Transforming Manufacturing
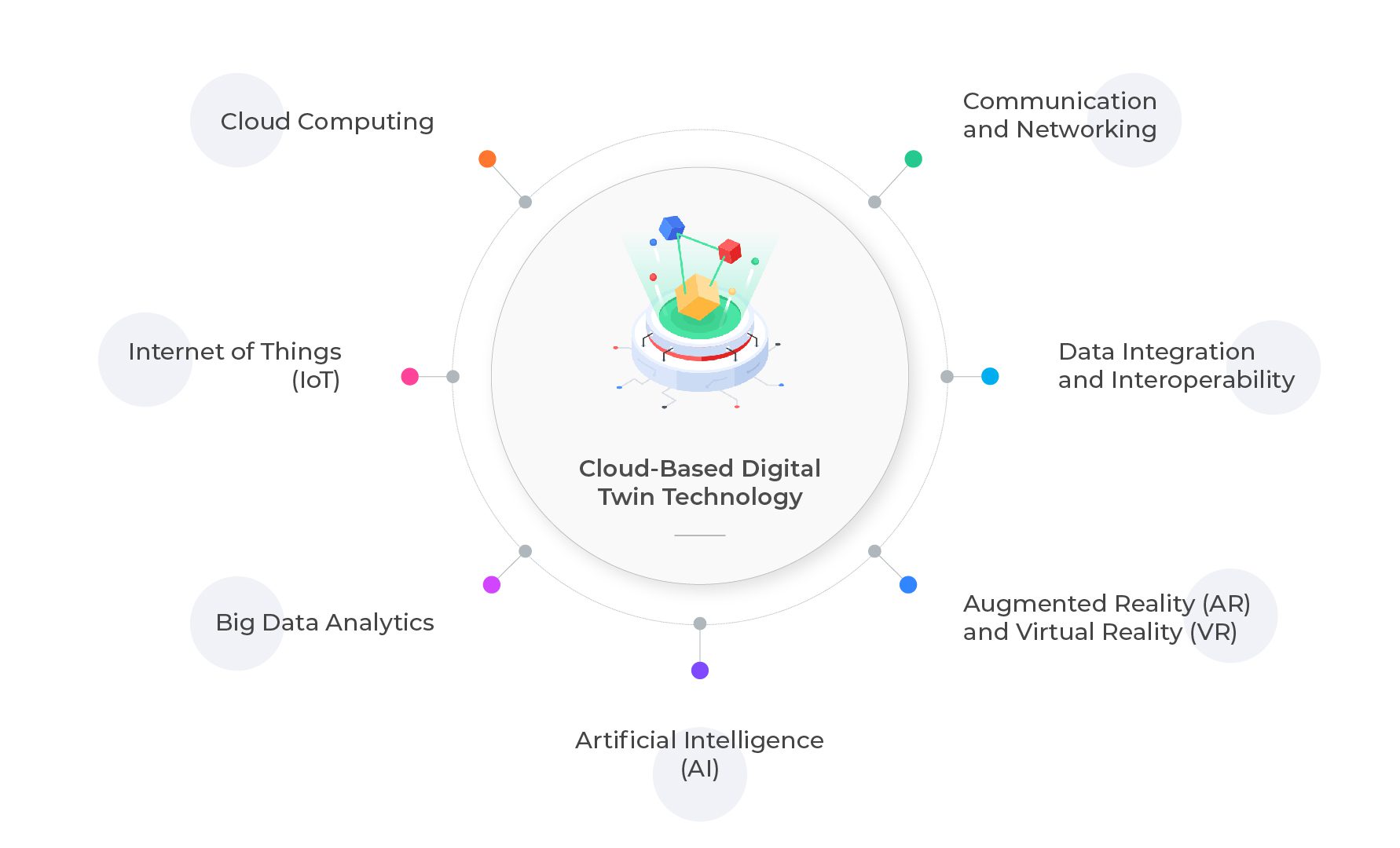
- Cloud Computing: Cloud-based digital twins utilize cloud computing infrastructure to store and process data. Cloud platforms provide the scalability, flexibility, and computational power required for managing large volumes of data, running complex simulations, and performing advanced analytics. Examples of popular cloud platforms include Amazon Web Services (AWS), Microsoft Azure, and Google Cloud Platform.
- Internet of Things (IoT): IoT plays a crucial role in cloud-based digital twins by connecting physical assets, equipment, and sensors to the digital twin. IoT devices and sensors collect real-time data from the physical world and transmit it to the cloud, where it is used to update and maintain the digital twin’s state. This data includes various parameters such as temperature, pressure, vibration, energy consumption, and more.
- Big Data Analytics: Digital twins generate and handle vast amounts of data from different sources. Big data analytics technologies are used to process and analyze this data to extract meaningful insights. Techniques such as data mining, machine learning, and statistical analysis are applied to identify patterns, correlations, and anomalies within the data. These insights help in optimizing processes, predicting maintenance needs, and improving overall performance.
- Artificial Intelligence (AI): AI techniques are employed in cloud-based digital twins to enable advanced functionalities such as predictive maintenance, anomaly detection, optimization, and autonomous decision-making. Machine learning algorithms can analyze historical and real-time data to make predictions, identify abnormal behavior, and generate recommendations for optimizing operations. AI enhances the intelligence and decision-making capabilities of digital twins.
- Augmented Reality (AR) and Virtual Reality (VR): AR and VR technologies are used to visualize and interact with digital twins in a more immersive way. By overlaying virtual information on the physical world or creating virtual environments, AR and VR allow users to explore and interact with digital twin representations. This enhances the understanding of complex systems, aids in training and troubleshooting, and supports collaborative decision-making.
- Data Integration and Interoperability: Cloud-based digital twins often need to integrate data from multiple sources and systems. This involves connecting various databases, enterprise resource planning (ERP) systems, manufacturing execution systems (MES), and other software applications. Data integration and interoperability technologies ensure smooth data flow between different systems, enabling a holistic view and accurate representation of the physical assets in the digital twin.
- Communication and Networking: Cloud-based digital twins rely on robust communication networks to transmit data between the physical assets and the cloud infrastructure. This includes wired and wireless networks, protocols, and standards that facilitate reliable and secure data transfer. Technologies like MQTT, OPC UA (Unified Architecture), and RESTful APIs are commonly used for efficient and standardized communication.
By leveraging cloud-based digital twin technology, manufacturers can simulate, optimize, and predict with greater efficiency and accuracy. This empowers them to make data-driven decisions, optimize operations, improve product quality, and achieve a competitive edge in the dynamic manufacturing landscape. Cloud computing continues to play a pivotal role in enabling the widespread adoption and success of digital twin technology in the manufacturing industry.
5 Advantages of Cloud-Based Digital Twin Technology
Cloud-based digital twin technology has some awesome benefits for the manufacturing industry! It’s like having a virtual replica of your physical assets in the cloud, and it can do some really cool things. Let us break it down for you:
First up is operational efficiency. With digital twins, manufacturers can keep a close eye on their real-time data and analyze it to find any inefficiencies in their operations. Imagine having a twin that tells you exactly where things are going wrong on your production line. For example, let’s say you have a manufacturing plant that uses digital twin technology. The digital twin monitors the performance of your production line in real-time and identifies bottlenecks. It then suggests adjustments to increase efficiency and reduce downtime. That means smoother operations and more products rolling off the line! According to Deloitte, using digital twin technology can boost equipment efficiency by up to 20% and slash maintenance costs by up to 50%. That’s a significant improvement, right?
Next, we have predictive maintenance. Digital twins use real-time data and fancy analytics to predict when your equipment might break down. This helps you plan maintenance schedules in advance, avoiding costly downtime. Picture this: you have a digital twin of a machine that collects and analyzes sensor data. It can predict when a component might fail and alert maintenance personnel in advance. This proactive approach allows for repairs or replacements to be made before the equipment breaks down, saving you from unexpected production halts and keeping everything running smoothly. In fact, MarketsandMarkets predicts that the predictive maintenance market, driven by digital twin technology, will reach a whopping $10.7 billion by 2024, growing at a rate of 28.4%. That’s a lot of savings and peace of mind!
But wait, there’s more! Digital twins also allow for virtual testing and optimization. Instead of building physical prototypes, you can simulate and test your manufacturing processes in a virtual environment. This saves time and resources. Let’s take an automotive manufacturer as an example. They create a digital twin of a new car model and simulate its performance under various conditions. This virtual testing helps them identify areas for improvement, such as aerodynamics or engine efficiency. By making adjustments in the virtual world, they can create a more efficient and reliable final product without the need for multiple physical prototypes. According to PTC, using digital twins for simulation and testing can reduce time-to-market by 30% and cut the number of physical prototypes by half. Imagine being able to fine-tune your designs and catch any issues before even lifting a wrench!
Another fantastic benefit is enhanced product quality. By continuously monitoring and analyzing data from your assets, digital twins help you catch quality issues early on. This means fewer defects and happier customers. Imagine this: you have a digital twin that monitors the manufacturing parameters of your product and compares them to predefined quality thresholds. If any deviations occur, the system alerts operators to take corrective actions. This ensures that only high-quality products make it to your customers, improving customer satisfaction and loyalty. An IBM survey found that companies using digital twins for quality management achieved a 25% reduction in defects and a 25% improvement in customer satisfaction. That’s a win-win!
Lastly, digital twins can revolutionize supply chain management. By keeping tabs on inventory levels, demand patterns, and logistical operations, they help you plan and coordinate your supply chain better. For example, imagine a digital twin that monitors the inventory levels of raw materials and components in real-time. By integrating with demand forecasting systems, it helps optimize inventory levels, reducing carrying costs while ensuring timely availability. This means you have the right materials at the right time, avoiding stockouts and keeping your production on track. In fact, Capgemini found that 76% of manufacturers believe digital twins will be essential to their supply chain operations in the next five years. It’s like having a super-smart twin who can optimize your inventory levels and make sure everything runs smoothly.
Looking ahead, the future holds immense potential for cloud-based digital twin technology. As emerging technologies such as artificial intelligence and machine learning continue to evolve, they will further enhance the capabilities of digital twins. Imagine self-optimizing production lines and predictive quality control. The possibilities are endless, and manufacturers must stay ahead of the curve to remain competitive.
Here are some real-world examples that show how digital twins can be applied in everyday scenarios, making manufacturing more efficient, reliable, and customer-centric.
- Bosch: Bosch, a leading global supplier of technology and services, has implemented cloud-based digital twins in its manufacturing processes. By utilizing Siemens MindSphere and Azure Digital Twins, Bosch has developed virtual replicas of their production lines and equipment. These digital twins enable them to monitor real-time data, optimize operations, and improve efficiency across their manufacturing facilities.
- Honeywell: Honeywell, a multinational conglomerate specializing in industrial technologies, has leveraged cloud-based digital twin technology to enhance their manufacturing operations. Through their Connected Performance Services (CPS) platform, Honeywell combines real-time data from sensors and equipment with digital twin simulations. This integration enables predictive maintenance, process optimization, and operational improvements, delivering significant value to their customers.
- BMW: BMW, a renowned automotive manufacturer, has embraced cloud-based digital twin technology to optimize its production processes. By implementing Siemens’ Xcelerator portfolio and utilizing Azure Digital Twins, BMW creates virtual replicas of their manufacturing systems, enabling simulation and optimization. These digital twins have helped BMW streamline operations, improve quality control, and reduce production costs.
- Rolls-Royce: Rolls-Royce, renowned for its aerospace and marine engineering solutions, has implemented cloud-based digital twins to transform its maintenance and servicing operations. Their digital twins integrate data from engines and aircraft systems, enabling predictive maintenance and optimizing fuel efficiency. Rolls-Royce’s digital twin technology has led to significant cost savings, improved safety, and enhanced overall performance for its customers.
- Procter & Gamble (P&G): P&G, a global consumer goods company, has adopted cloud-based digital twin technology to optimize its manufacturing processes. By leveraging Siemens’ digital twin solutions, P&G creates virtual replicas of their production lines, allowing for real-time monitoring and optimization. This digital twin implementation has resulted in improved operational efficiency, reduced costs, and enhanced agility in responding to market demands.
Microsoft Azure: Your Partner of Choice
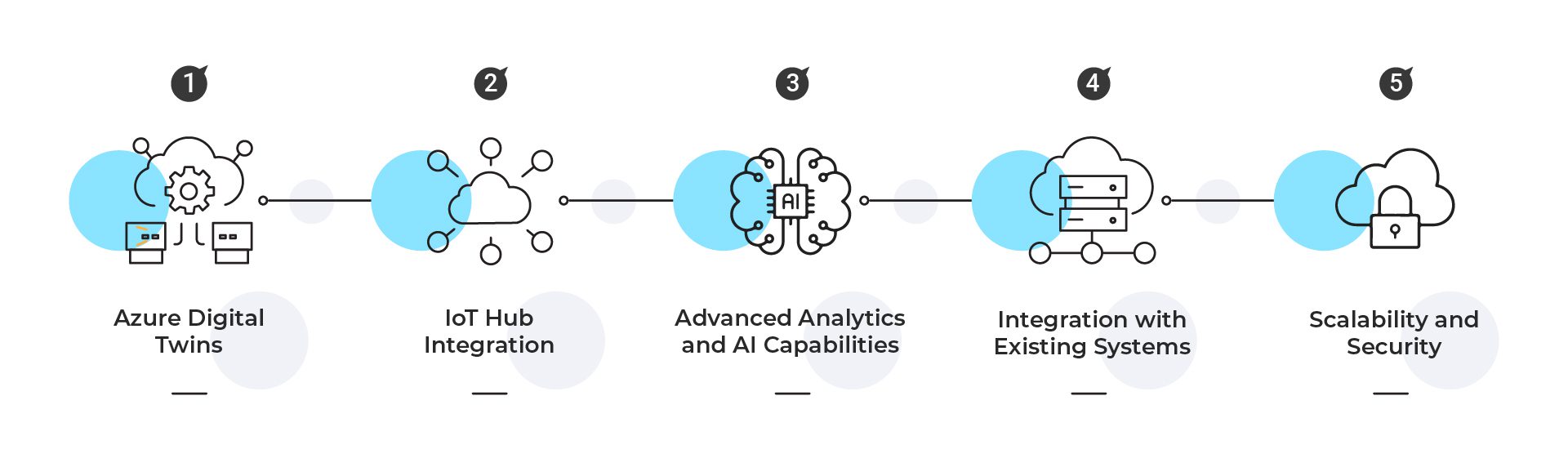
Microsoft Azure offers a range of services and tools that can assist companies in implementing cloud-based digital twin technology within their organization. Here are some ways Microsoft Azure can help:
- Azure Digital Twins: Azure Digital Twins is a platform provided by Microsoft that allows companies to create and manage digital twins of their physical assets and environments. It provides a scalable and flexible cloud infrastructure to model, simulate, and monitor the behavior of assets in real time. Azure Digital Twins simplifies the development and deployment of digital twins, enabling companies to focus on utilizing the technology for optimization, analytics, and decision-making.
- IoT Hub Integration: Azure IoT Hub, another offering by Microsoft Azure, seamlessly integrates with Azure Digital Twins. This integration allows companies to connect IoT devices and sensors to their digital twins, capturing real-time data from physical assets. By combining the power of IoT and digital twins, companies can monitor and analyze the performance of their assets, enabling predictive maintenance, optimizing operations, and improving overall efficiency.
- Advanced Analytics and AI Capabilities: Microsoft Azure provides a wide range of advanced analytics and artificial intelligence (AI) tools that can be leveraged in conjunction with digital twin technology. Azure Machine Learning, Azure Cognitive Services, and Azure Data Lake Analytics are just a few examples of services available. These tools enable companies to perform sophisticated data analysis, implement predictive modeling, and derive valuable insights from the data collected through digital twins.
- Integration with Existing Systems: Microsoft Azure offers robust integration capabilities, allowing companies to connect their digital twins with their existing systems, applications, and data sources. This integration ensures that the digital twin technology becomes an integral part of the company’s overall infrastructure and workflows, enhancing data sharing, collaboration, and decision-making across the organization.
- Scalability and Security: Azure’s cloud infrastructure provides scalability, allowing companies to dynamically adjust their resources and accommodate the growing needs of their digital twin implementations. Additionally, Azure offers robust security measures and compliance standards to protect the sensitive data collected and stored within digital twin systems. This ensures that companies can confidently adopt cloud-based digital twin technology while maintaining the highest standards of data security and privacy.
Microsoft Azure’s comprehensive suite of services and tools provides a solid foundation for companies to implement cloud-based digital twin technology. It simplifies the development, deployment, and integration of digital twins while offering advanced analytics, scalability, and security. With Azure, companies can leverage the full potential of digital twins to optimize operations, improve asset performance, and drive innovation within their organizations.
The Data Dynamics Advantage
Microsoft has taken strides to simplify the migration journey with the Azure File Migration Program. By leveraging Data Dynamics’ StorageX, organizations can effortlessly migrate unstructured files and object storage data into Azure without incurring any additional costs or licensing requirements. It’s as easy as registering your migration project details with Data Dynamics and commencing data movement immediately.
StorageX, renowned as Data Dynamics’ leading unstructured data migration software, offers automated policy-based data migration. With StorageX, you can seamlessly migrate data to the cloud, consolidate data centers, and optimize storage, enabling intelligent, swift, and secure petabyte-scale unstructured data migrations. The collaboration between Microsoft and Data Dynamics in this program aims to help organizations tackle critical challenges they face during the cloud migration lifecycle, including cost, speed, talent, and risk.
Get ready to be part of this extraordinary journey where cloud-based digital twins reshape the manufacturing landscape. The potential for progress and growth knows no bounds as we harness the power of these twins to drive innovation, sustainability, and collaboration. It’s a future full of possibilities, and we’re just getting started.
To explore how Data Dynamics can assist you in venturing into the cloud with Azure, visit our website at www.datadynamicsinc.com. For further inquiries or to discuss your specific needs, you can reach out to us via email at solutions@datdyn.com or give us a call at (713)-491-4298 or +44-(20)-45520800. Our dedicated team is ready to provide you with comprehensive information about our cutting-edge data management solutions.
To know more about Data Dynamics can help you take the plunge into cloud with Azure, visit www.datadynamicsinc.com/microsoft/ or contact us at solutions@datdyn.com or call us at (713)-491-4298 or +44-(20)-45520800. It’s your one-stop destination to discover more about our cutting-edge offerings in the world of data management.