Highlights:
- The manufacturing sector is experiencing a rapid shift toward automation, transforming it from a discretionary choice to an imperative for businesses seeking a competitive edge in the evolving market.
- Cobots are rapidly becoming indispensable in manufacturing due to their transformative impact on efficiency, flexibility, and safety. They collaborate with human workers, enhancing productivity by handling repetitive tasks and allowing professionals to focus on intricate aspects of production.
- Beyond their traditional roles, cobots excel in diverse applications such as 3D printing support, precision machine tending, collaborative welding, data-driven quality control, and warehousing/logistics, contributing to a more agile and responsive industrial landscape.
- Microsoft Azure emerges as a key partner for manufacturing companies adopting cobots. Its cloud-based services facilitate IoT integration, data analytics, security, scalability, and collaboration with productivity tools, providing a robust foundation for cobotic systems.
- Microsoft Azure, in collaboration with Data Dynamics, introduces the Azure File Migration Program. This program offers a ZERO-cost migration solution for manufacturing data to Azure, addressing challenges such as manual processes and budget constraints.
In this Quick-Byte:
In the evolving landscape of manufacturing, collaborative robots, or cobots powered by Microsoft Azure, are reshaping operations by seamlessly integrating them into automated processes. These versatile robots, with their ability to undertake various tasks alongside human workers, enhance efficiency, flexibility, and safety. The blog explores the transformative impact of cobots, their lesser-known applications, and how Microsoft Azure provides a robust foundation for their integration. Additionally, it delves into the pivotal role of data in cobotic systems, emphasizing the importance of Unified Data Management (UDM) for effective data utilization. It highlights the combined efforts of these technologies, setting the stage for an intelligent, adaptive, and data-driven future in manufacturing.
Redefining Manufacturing Through Cobots: A Paradigm Shift in Automation
The manufacturing landscape is undergoing a rapid and undeniable transformation through the pervasive influence of automation. Industrial automation is no longer a discretionary consideration or a futuristic concept reserved for sophisticated operations. It has swiftly evolved into an imperative for businesses aiming to sustain a competitive advantage in the evolving market. Within this era of heightened automation, manufacturing cobots, or collaborative robots, emerge as an ideal fit. These versatile robots are well-suited to integrate into the advanced fabric of automated processes seamlessly. Whether for large corporations or small businesses, cobots offer a means to expand and automate operations within factories, warehouses, and research facilities. What sets collaborative robots apart is their capability to undertake repetitive, hazardous, or precision-demanding tasks side by side with human workers.
What are Cobots? How are they revolutionizing the manufacturing sector?
Collaborative robots, often referred to as cobots, represent a specialized category within industrial robotics designed for safe and effective collaboration with human workers. In contrast to traditional large and expensive industrial robots, cobots distinguish themselves with their compact size, reduced weight, and affordability. Their user-friendly programming interface makes them well-suited for various manufacturing and assembly tasks. While early versions of cobots were relatively simple, advancements in sensors, artificial intelligence, and robotics have elevated them to a level of sophistication far beyond their humble beginnings.
In manufacturing, cobots have become indispensable, reshaping operational dynamics by significantly impacting efficiency, flexibility, and safety. Unlike traditional robots, cobots seamlessly collaborate with human workers, boosting productivity by handling repetitive tasks and allowing professionals to focus on intricate aspects of production. Their inherent adaptability enables easy programming and reprogramming to swiftly meet changing production requirements. This flexibility, combined with advanced safety features, addresses industry challenges related to workforce dynamics and the need for secure working environments.
Cobots play a crucial role in democratizing automation, extending its benefits to small and medium-sized enterprises. Their affordability and easy integration empower businesses of various sizes to leverage cutting-edge manufacturing technologies. Beyond their automation role, cobots foster a culture of collaborative innovation within manufacturing entities. Human workers engage in synergistic partnerships with these robots to optimize processes, identify improvement areas, and implement inventive solutions. This growing demand for cobots signifies a shift in manufacturing, where the harmonious interplay of human intuition and robotic precision creates adaptive, efficient, and sustainable production environments.
Since their introduction in 2008, collaborative robots, or cobots, have experienced a significant surge in adoption within the manufacturing landscape. This surge is undeniably attributed to the capacity of cobots to enhance efficiency and productivity for human workers by simplifying daily tasks. Unlike their industrial counterparts, cobots offer a streamlined and less labor-intensive setup, making them an appealing choice for manufacturers seeking agile automation solutions. The International Federation of Robotics projects an annual growth rate of 40%, while Interact Analysis anticipates that cobot revenues will achieve an impressive $1.94 billion by 2028, constituting 15.7% of the overall robot market.
5 Lesser Known Applications of Cobots in the Manufacturing Industry
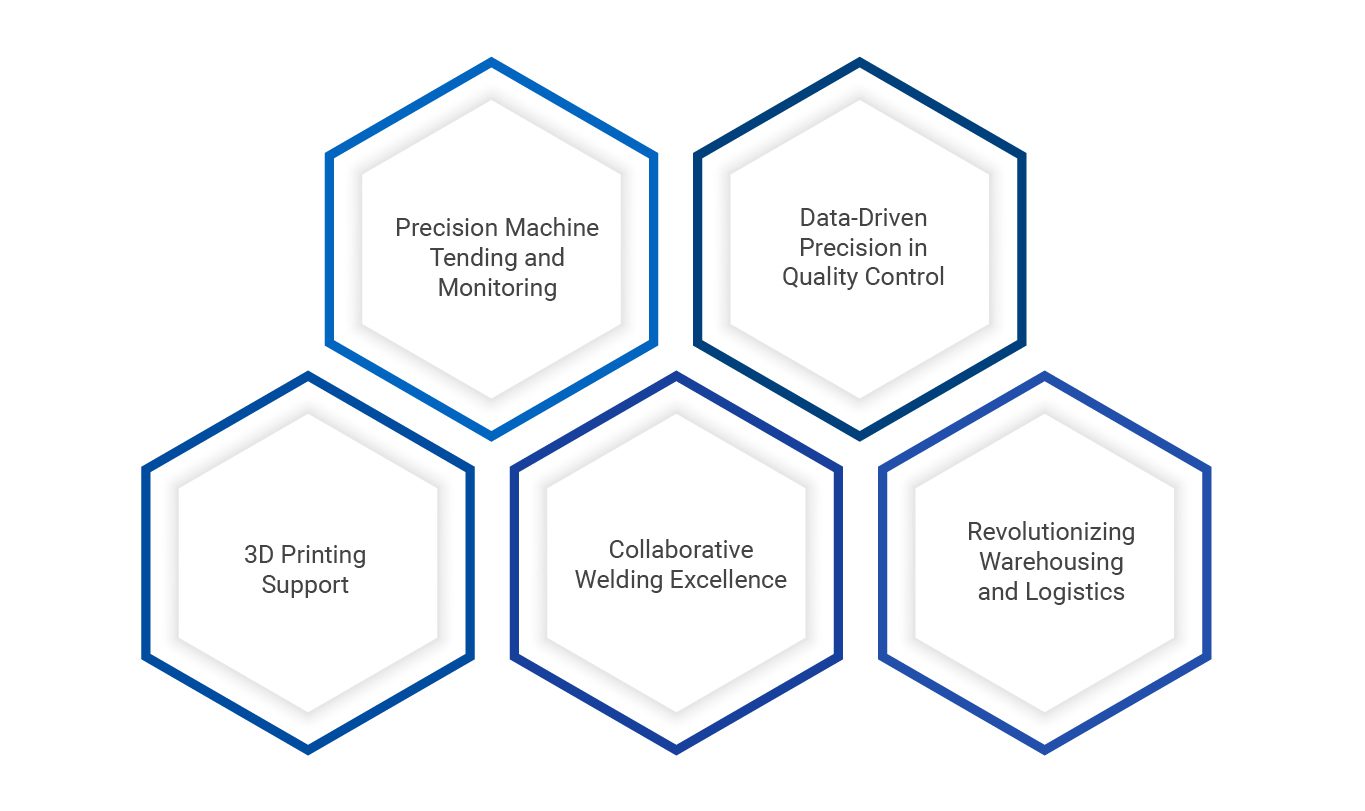
3D Printing Support: Equipped with advanced features like vision sensors and force feedback algorithms, they handle intricate tasks such as automated filament loading and unloading. Their precise sensors ensure accurate filament positioning, leading to consistent printing quality and reduced material waste. Cobots also contribute to the removal of support structures, delicately extracting them without harming the finished print, thus saving manual labor and reducing the risk of print failures. Additionally, they integrate polishing or sanding tools for refined surface finishes, automating post-processing and enhancing the cosmetic appeal of 3D-printed objects. A study by Deloitte and the Manufacturing Leadership Council predicts an 80% increase in 3D printing adoption over the next five years, with cobots playing a crucial role in driving this growth.
Precision Machine Tending and Monitoring: Cobots with high-precision grippers and advanced vision systems handle the loading and unloading of workpieces onto CNC machines with exceptional accuracy. They surpass human capabilities, minimizing product defects and integrating sensor technologies for anomaly detection in machine performance. Through AI-powered monitoring, cobots analyze sensor data with a 95% accuracy rate, predicting potential failures and enabling preventive maintenance. This proactive approach reduces unplanned downtime by up to 50%. Advanced cobots also feature automatic tool-changing mechanisms, enhancing production agility by 20% and enabling the flexible and seamless production of diverse parts.
Collaborative Welding Excellence: Cobots excel in collaborative welding, showcasing agile movements and precise control with impressive repeatability. Equipped with lightweight arms and advanced sensors, they contribute to a 70% reduction in scrap rates attributed to welding errors. Serving as invaluable assistants to human welders, cobots assist in positioning components, steadying pieces, and managing cables, freeing up human welders for higher-value tasks. This collaborative approach significantly boosts overall productivity by 30%. Cobots prioritize safety with features such as collision detection sensors, emergency stop buttons, and built-in safety zones, leading to an 80% reduction in workplace accidents during collaborative welding.
Data-Driven Precision in Quality Control: Armed with high-resolution vision systems and advanced AI algorithms, excel in detecting minute defects on products with unparalleled accuracy. They surpass human visual inspection capabilities, identifying misalignments, surface imperfections, or missing components with a 99.9% accuracy rate. Cobots use real-time data analysis for immediate adjustments to production processes, machine settings, or robot movement parameters, resulting in a continuous improvement approach and a substantial 15% reduction in overall defect rates. By seamlessly integrating with manufacturing execution systems (MES), cobots provide real-time data on each product, ensuring complete traceability throughout the production process, empowering enhanced quality control measures, and facilitating streamlined product recalls in the event of issues.
Revolutionizing Warehousing and Logistics: Cobots are reshaping operations with their high payload capacity, reducing physical strain on human workers and enhancing overall productivity. Leveraging 3D cameras and advanced AI algorithms, they excel in pick-and-place operations with depth perception, effectively locating and retrieving items from diverse shelf configurations, even in cluttered or poorly lit environments. Collaborating with human packers, cobots contribute to order packing tasks, reducing processing times and minimizing errors. Market projections indicate a Compound Annual Growth Rate (CAGR) of 45.2% in the warehouse cobot market between 2022 and 2027, reflecting the transformative impact of cobots on warehouse efficiency and worker safety.
Microsoft Azure: Your Partner of Choice
Microsoft Azure offers a comprehensive suite of cloud-based services and solutions that can significantly support manufacturing companies in adopting and optimizing the use of cobots. Here are several ways in which Azure can assist in the integration and management of cobotic systems in the manufacturing sector:
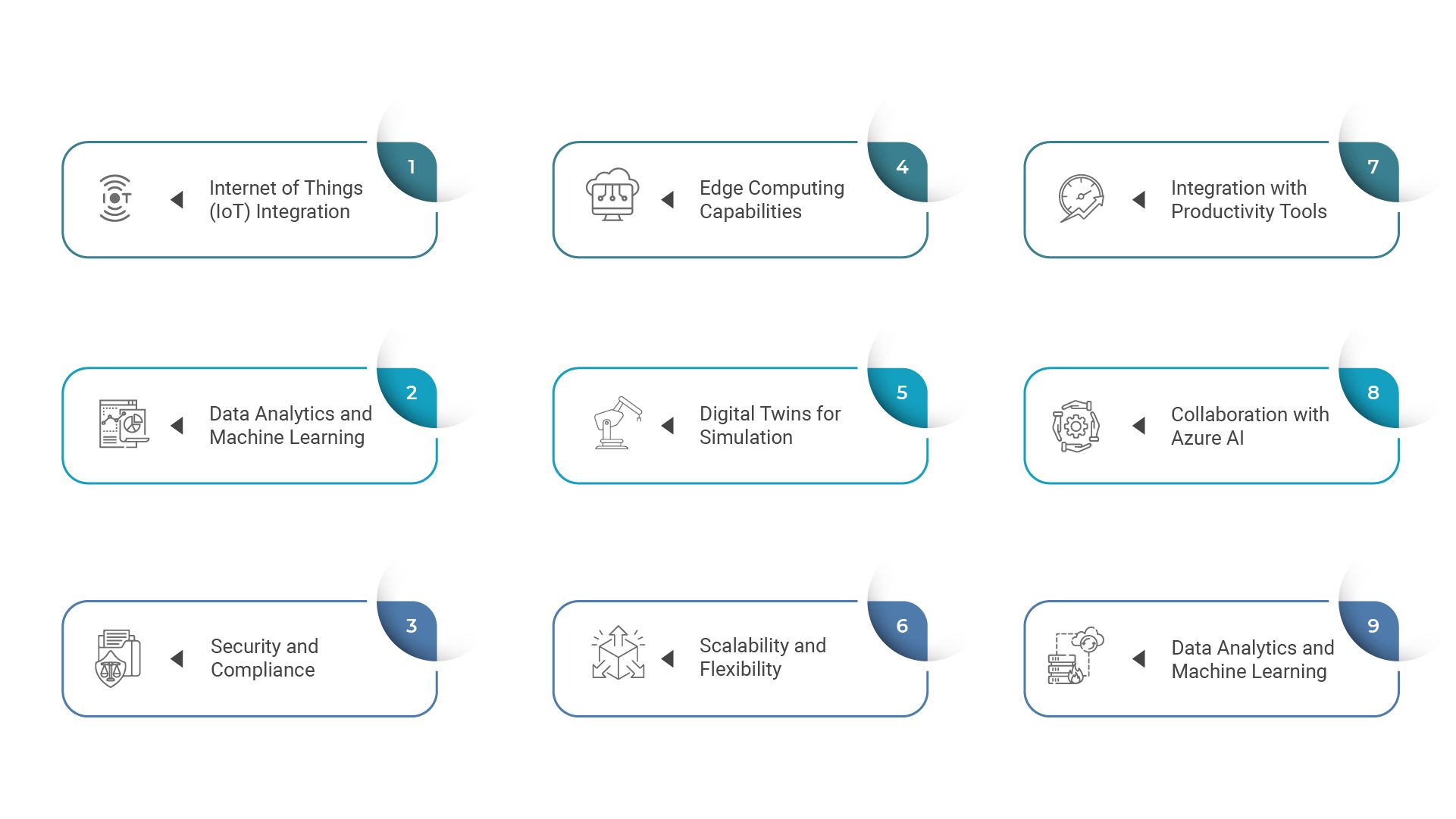
- Internet of Things (IoT) Integration: Azure IoT services enable seamless connectivity and integration of cobots into the broader manufacturing ecosystem. By leveraging Azure IoT Hub, manufacturers can collect, analyze, and act upon real-time data generated by cobots. This facilitates remote monitoring, predictive maintenance, and data-driven decision-making.
- Data Analytics and Machine Learning: Azure’s advanced analytics and machine learning services empower manufacturers to derive actionable insights from the vast amount of data generated by cobots. By applying machine learning algorithms, manufacturers can optimize production processes, predict equipment failures, and enhance overall operational efficiency.
- Security and Compliance: Azure provides robust security features to safeguard cobotic systems and the data they generate. With features like Azure Security Center and Azure Policy, manufacturers can implement and enforce security best practices, ensuring the integrity, confidentiality, and compliance of cobot-related data.
- Edge Computing Capabilities: Azure extends its capabilities to the edge, allowing manufacturers to deploy edge computing solutions. This is particularly beneficial for scenarios where real-time processing of cobot data is crucial. Edge computing reduces latency, enabling quicker decision-making and enhancing the responsiveness of cobotic systems.
- Digital Twins for Simulation: Azure Digital Twins allows manufacturers to create digital representations of physical manufacturing environments, including cobotic workflows. This enables simulation and testing of cobot behaviors and interactions before implementation, minimizing disruptions and optimizing system performance.
- Scalability and Flexibility: Azure’s cloud infrastructure provides scalability and flexibility, allowing manufacturers to scale their cobotic deployments based on changing production demands. This ensures that the manufacturing system remains adaptable and responsive to fluctuations in market requirements.
- Integration with Productivity Tools: Azure seamlessly integrates with Microsoft’s suite of productivity tools, such as Microsoft 365 and Power Platform. This integration enables manufacturers to incorporate cobotic data into broader business workflows, facilitating collaboration, reporting, and decision-making across different departments.
- Collaboration with Azure AI: Azure AI services can enhance the capabilities of cobots. By integrating Azure AI, manufacturers can enable cobots to perform more advanced tasks, such as image recognition, natural language processing, and other AI-driven functions, expanding their utility in diverse manufacturing scenarios.
- Backup and Disaster Recovery: Azure’s backup and disaster recovery services provide manufacturers with reliable mechanisms to safeguard cobot-related data. This ensures business continuity in the event of unforeseen disruptions or data loss incidents.
By leveraging these Azure services, manufacturing companies can build a robust and scalable foundation for the adoption of cobots, enhancing operational efficiency, data-driven decision-making, and overall competitiveness in the evolving manufacturing landscape. However, one of the common dilemmas faced in this journey is the formidable challenge of migrating and managing data from legacy systems to the cloud. Let’s decipher why.
Data: The Foundation for Collaborative Robots
In the fast-paced world of manufacturing, where collaborative robots (cobots) are taking center stage, the importance of data cannot be overstated. These intelligent machines, designed to work seamlessly alongside humans, rely heavily on a steady influx of information to navigate their surroundings, make informed decisions, and adapt to dynamic environments. The utilization of data is not merely an accessory to the functionality of Cobots; rather, it is their lifeblood, shaping their responsiveness, precision, and overall effectiveness.
One of the key challenges faced by organizations in deploying Cobots stems from the nature of data itself, particularly when it is unstructured which accounts for 80% of enterprise data, according to IDC. Unstructured data, characterized by its lack of a predefined data model or organizational schema, poses a significant hurdle to the seamless integration of Cobots into various workflows. The diversity of formats, sources, and types within unstructured data makes it difficult for traditional automation systems to extract meaningful insights. This challenge is further exacerbated when attempting to implement Cobots in environments where data sources are diverse and constantly evolving. The impact of struggling with unstructured data is tangible, with Accenture estimating an annual cost of around $140 billion incurred by organizations in terms of wasted time and resources.
For organizations aiming to unlock the full potential of Cobots, the analysis of unstructured data becomes imperative. Without a robust strategy for handling and deriving value from this data, the capabilities of Cobots are severely limited. Moreover, unstructured data often contains invaluable information that, if properly harnessed, can enhance the adaptability and intelligence of Cobots, enabling them to perform tasks with greater efficiency and precision.
In response to these challenges, organizations are increasingly turning to Unified Data Management (UDM) solutions. UDM serves as a comprehensive framework that integrates, manages, and analyzes both structured and unstructured data. By adopting UDM, organizations can establish a cohesive data ecosystem that allows for seamless communication between different data sources and ensures that valuable insights are not lost in the vast sea of unstructured information. UDM acts as a bridge, connecting disparate data sets and providing a unified view that Cobots can leverage to enhance their decision-making processes. This holistic approach to data management not only addresses the challenges associated with unstructured data but also empowers organizations to harness the full potential of Cobots in dynamic and evolving work environments.
For manufacturers navigating the complexities of unstructured data in the era of cobots, integrating UDM with Azure services becomes not just an option but a strategic necessity. This dynamic duo addresses the formidable challenge of migrating and managing data from legacy systems to the cloud.
The Data Dynamics Advantage
Data Dynamics’ Unified Unstructured Data Management software is a game-changer for manufacturers looking to migrate and manage their legacy unstructured data effectively. Microsoft, in collaboration with Data Dynamics, introduces the Azure File Migration Program tailored for enterprises seeking a ZERO-cost migration of their manufacturing data to Azure. This collaboration addresses challenges such as manual processes and budget constraints that often impede cloud initiatives.
The Azure File Migration Program offers a transformative solution, enabling organizations to seamlessly migrate unstructured files and object storage data to Azure without incurring additional costs or migration license concerns. Employing a policy-based migration process, the solution not only reduces risks but also ensures granular control over access and file security, preserving the integrity of manufacturing data. Organizations can register their migration projects with Data Dynamics, initiating the smooth movement of manufacturing data to Azure promptly.
Beyond data migration, the collaboration between Microsoft and Data Dynamics emphasizes intelligent data management across On-Premise, Azure, and Hybrid Cloud environments, enhancing overall efficiency. Data Dynamics stands out with its Unified Data Management (UDM) software designed for intelligent, data-driven migration to Azure. Notably, the software’s petabyte-scale capability is specifically tailored for manufacturing operations across Azure File, Azure Netapp, Azure Blob, and OneDrive, distinguishing it from solutions geared toward smaller environments.
Data Dynamics prioritizes enhanced data compliance and security through its migration module, seamlessly integrated with Microsoft Information Protection and Azure Information Protection. Geo-specific migration adheres to data sovereignty regulations, ensuring compliance with regional data requirements. Importantly, Data Dynamics ensures that manufacturing data remains accessible and usable without unnecessary restrictions, avoiding data hostage situations.
With a focus on modern enterprise needs, Data Dynamics offers a unified platform for enterprise data management that scales seamlessly across hybrid, multi-cloud, and legacy environments. This approach eliminates data silos, enhances efficiency, and provides unparalleled flexibility and future-proofing for clients aligning with the evolving demands of the business landscape.
To learn more, visit our website at www.datadynamicsinc.com/microsoft/. You can also contact us at solutions@datdyn.com or (713)-491-4298 or +44-(20)-45520800.