For years, manufacturing has been a catalyst for global prosperity and economic advancement. Technological advancements have revolutionized this industry, empowering it to become more intelligent and adaptable, ensuring its continued evolution alongside changing consumer requirements. As a result, industry pioneers have shifted their focus from conventional to smart factory technology. Smart factories offer a multitude of benefits to operators, managers, and executives within the manufacturing sector. However, despite these advantages, a handful of companies remain hesitant to embark on their smart journey. This article delves into the perks of smart factories, outlining their disparities from traditional manufacturing methods. Moreover, it provides valuable insights into efficient data management while preparing to transition to smart factories, driving profitability and infrastructure optimization.
What is a ‘Smart Factory’?
The past decade has witnessed an extraordinary surge in technological advancements, reshaping industries across the board. From the emergence of the Internet of Things (IoT) to the availability of vast computing power and breakthroughs in artificial intelligence (AI), manufacturers have been presented with boundless opportunities. Consequently, the notion of smart factories has transcended the realm of distant aspirations and become an achievable reality. But what exactly defines a smart factory? Picture a manufacturing facility endowed with the ability to think, learn, and autonomously adapt to changes. This encapsulates the essence of a smart factory—a cutting-edge environment where advanced technologies such as IoT, AI, and data analytics converge to establish a seamlessly interconnected and highly efficient production ecosystem.
This paradigm shift, commonly referred to as Industry 4.0 or the fourth industrial revolution, drives the digital transformation of the manufacturing industry. It entails the integration of intelligent machines and systems that communicate seamlessly with each other and with humans in real-time. The overarching goal is to cultivate a manufacturing process that embodies agility, efficiency, and a customer-centric approach.
So, why is the industry gravitating toward smart factories? Well, the advantages they offer are quite compelling. Let’s explore some of the key benefits:
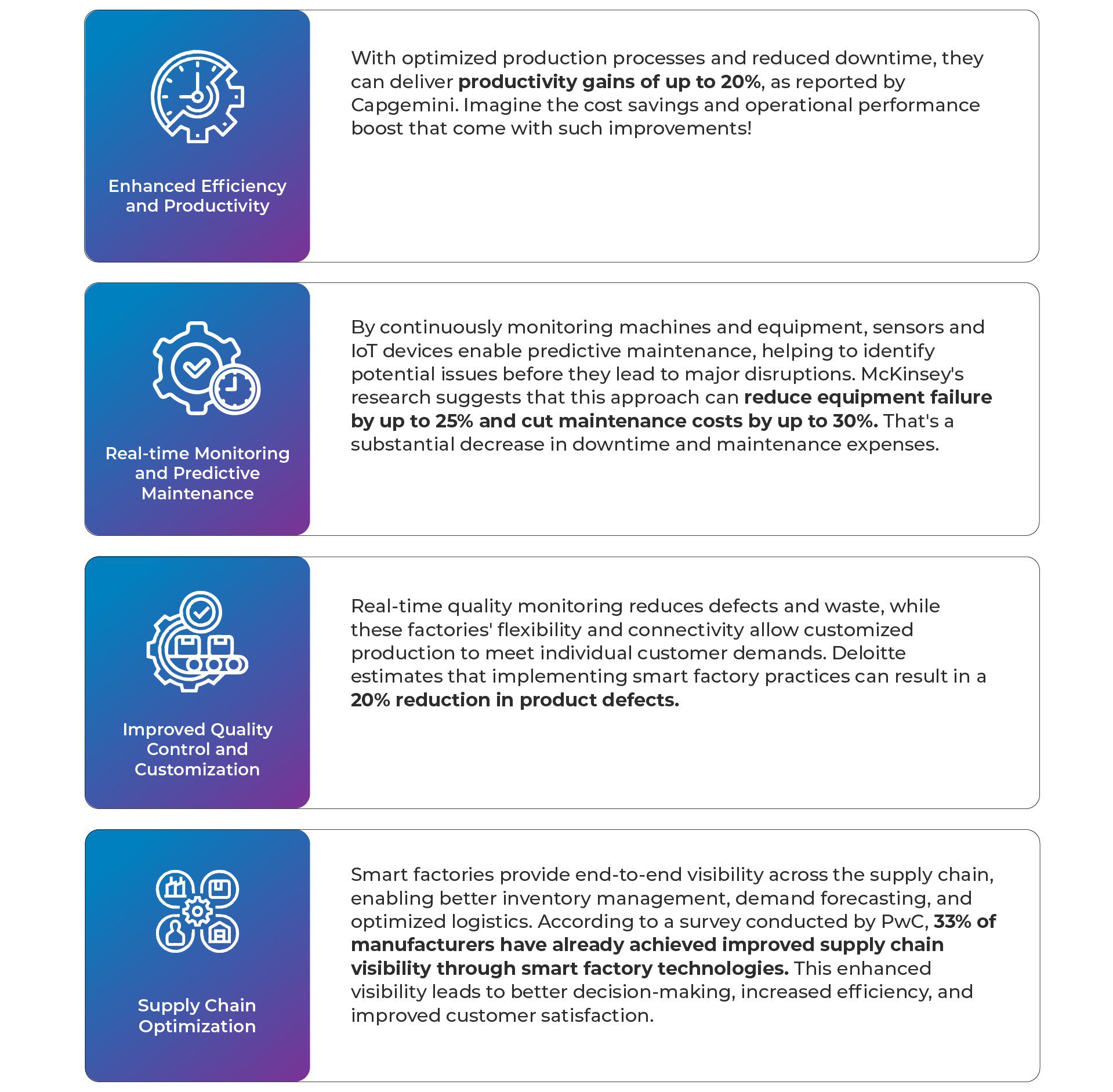
Smart factories are the next frontier in manufacturing, driven by the emergence of advanced technologies and the need for increased efficiency. Industry 4.0 is propelling this shift towards smart factories, offering advantages such as enhanced productivity, real-time monitoring, improved quality control, and optimized supply chain operations. Compared to traditional manufacturing, smart factories bring automation, data-driven decision-making, and cost savings to the table.
Smart Factory vs. Traditional Manufacturing
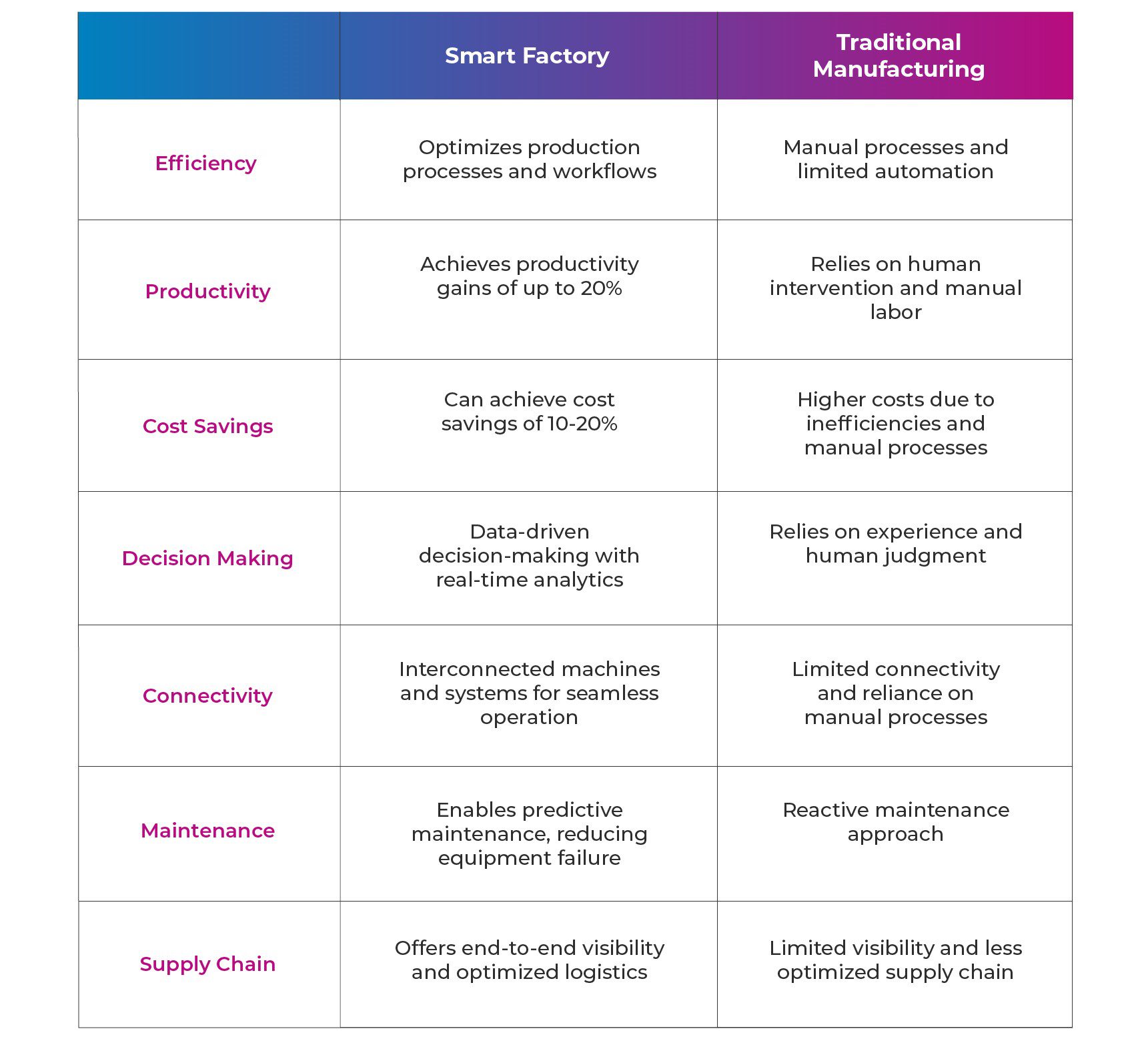
Here are some examples of companies utilizing Smart Factories:
- BMW: BMW, a renowned automobile manufacturer, has embraced the concept of smart factories to enhance their production processes. They utilize sensors and IoT devices across their manufacturing facilities to collect real-time data on machine performance, energy consumption, and quality control. By integrating this data into a centralized system, BMW can monitor and analyze key metrics to optimize production efficiency and identify areas for improvement. For example, they can detect anomalies in machine behavior, predict maintenance needs, and adjust production schedules accordingly. This data-driven approach enables BMW to achieve higher productivity, reduce downtime, and improve overall product quality.
- Siemens: Siemens, a global technology conglomerate, has implemented smart factory solutions to manage the vast influx of data in their manufacturing operations. They leverage advanced analytics and AI algorithms to process and analyze real-time data from their production lines. By integrating machine, quality, and supply chain data, Siemens gains valuable insights into their operations. This enables them to optimize processes, streamline workflows, and identify potential bottlenecks or quality issues. Through the utilization of data-driven decision-making, Siemens has achieved significant improvements in production efficiency, quality control, and supply chain optimization.
- PepsiCo: PepsiCo, a multinational food and beverage company, has adopted smart factory technologies to manage the influx of data and drive operational excellence. They leverage IoT sensors and automation systems throughout their manufacturing facilities to collect data on production rates, equipment performance, and energy consumption. By integrating this data into a central platform, PepsiCo can monitor real-time production metrics and proactively address any issues that may arise. For instance, they can optimize machine utilization, reduce energy waste, and ensure product consistency and quality. Analyzing and acting upon data in real-time has allowed PepsiCo to enhance its manufacturing processes, improve resource efficiency, and meet customer demands more effectively.
- Foxconn: Foxconn, a global electronics manufacturer, has implemented smart factory technologies to manage the vast amount of data generated in their production processes. They leverage IoT sensors, machine learning algorithms, and real-time analytics to monitor and optimize their manufacturing operations. By collecting data on machine performance, product quality, and supply chain logistics, Foxconn gains insights into its production efficiency and can make data-driven decisions to enhance productivity. For example, they can analyze data to identify bottlenecks, optimize machine utilization, and improve production line workflows. Through effective data management, Foxconn has achieved higher operational efficiency, reduced costs, and improved overall product quality.
- Haier: Haier, a leading home appliance manufacturer, has embraced smart factory concepts to manage the influx of data and transform its manufacturing processes. They leverage IoT devices, cloud computing, and AI to collect and analyze data from their production lines, supply chain, and customer feedback. This enables Haier to monitor product performance, identify quality issues, and make continuous improvements. By integrating data from multiple sources, Haier can achieve end-to-end visibility across its manufacturing operations and supply chain. This empowers them to optimize production scheduling, improve resource allocation, and deliver customized products based on customer preferences. Through the utilization of smart factory technologies, Haier has achieved higher production efficiency, improved product quality, and enhanced customer satisfaction.
The remarkable success stories of leading global corporations highlight the transformative impact of Smart Factories. But what lies at the core of these innovative manufacturing hubs? It’s none other than data—the driving force behind their operation. Let’s delve deep into the pivotal role that data plays in fueling the implementation of smart factories, exploring its significance and impact on this revolutionary manufacturing paradigm.
Data is the Lifeblood of Smart Factories
Picture this: The foundation of a smart factory lies in the realm of data, and oh boy, has the generation of data evolved over time! Let’s take a trip down memory lane and explore how we’ve reached the era of data-driven manufacturing.
Back in the day, factories relied heavily on manual processes and limited data collection. It was all about human expertise and observation to keep things running smoothly. Data generation was primarily centered around basic metrics like production counts, material usage, and maybe a few handwritten logs. But then, technology started weaving its magic. With the advent of computers, automation, and connectivity, the generation of data took a quantum leap. The birth of the Internet of Things (IoT) opened the floodgates for a whole new level of data collection. Machines and sensors became our trusty allies, constantly churning out data like never before.
In today’s smart factories, data generation is at an all-time high, with upwards of 5 petabytes (PB) of data per week. Every machine, sensor, and device is a data-generating powerhouse that captures a vast array of data types, from structured data like production metrics to unstructured data like audio and video feeds. We’re talking about real-time metrics on machine performance, energy consumption, temperature, pressure, quality checks, and so much more. We’re living in a time where the influx of data is reaching mind-boggling levels. It’s like a data tsunami sweeping through the manufacturing landscape. But it’s not just about the quantity of data; the quality and variety truly make a difference.
Now, you might be wondering, with all this data pouring in, what could possibly go wrong? Well, let’s talk about the challenges that come hand in hand with this data deluge. One major challenge is data overload. Manufacturers are grappling with enormous volumes of data from diverse sources, making it a daunting task to process and extract meaningful insights from the vast sea of information. It’s like trying to find a needle in a haystack.
Data quality is another hurdle. With data streaming in from various sensors and devices, ensuring the accuracy and reliability of the data becomes crucial. Incomplete, inconsistent, or inaccurate data can lead to flawed analyses and misguided decision-making. Trust me, you don’t want to base your operations on faulty data.
And then there’s the issue of data integration. Data is generated and stored in silos in many manufacturing setups, scattered across different systems and departments. Bringing all this data together, connecting the dots, and gaining a holistic view of the entire manufacturing process can be a real headache. It’s like trying to assemble a puzzle without having all the pieces in one place.
It’s safe to conclude that while it brings many advantages, it also brings its own set of future challenges. As smart factories become more prevalent, the volume and complexity of data will only multiply. With a multitude of connected devices, sensors, and AI algorithms in play, the amount of data generated will soar to new heights. It’s like adding fuel to the data fire. Managing this explosion of data will require robust data infrastructure, scalable storage systems, and powerful analytics capabilities. Manufacturers will need to invest in advanced technologies like edge computing and cloud platforms to process, store, and analyze this massive influx of data in real time. It’s a race against time to keep up with the growing data demands. Moreover, with more data comes the need for enhanced data security and privacy. Protecting sensitive manufacturing data from cyber threats and ensuring compliance with regulations becomes even more critical. The smart factory will have to be fortified with robust cybersecurity measures to safeguard valuable data assets.
5 Ways How a Unified Data Management Platform Helps in the Journey to Smart Factories
In the journey towards smart factories, the role of an efficient and unified data management platform cannot be overstated. This article explores five crucial ways in which such a platform empowers organizations to navigate the path toward smart factory transformation. From streamlining data integration to enabling advanced analytics, these benefits highlight the significance of a unified data management approach in driving successful implementation and maximizing the potential of smart factories.
1. Seamless Data Integration
A unified data management platform acts as a central hub, seamlessly integrating data from various sources within the smart factory ecosystem. It consolidates data from production machines, IoT devices, supply chain systems, and other relevant sources, providing a holistic view of operations. This integration ensures a unified data foundation, enabling real-time insights and informed decision-making.
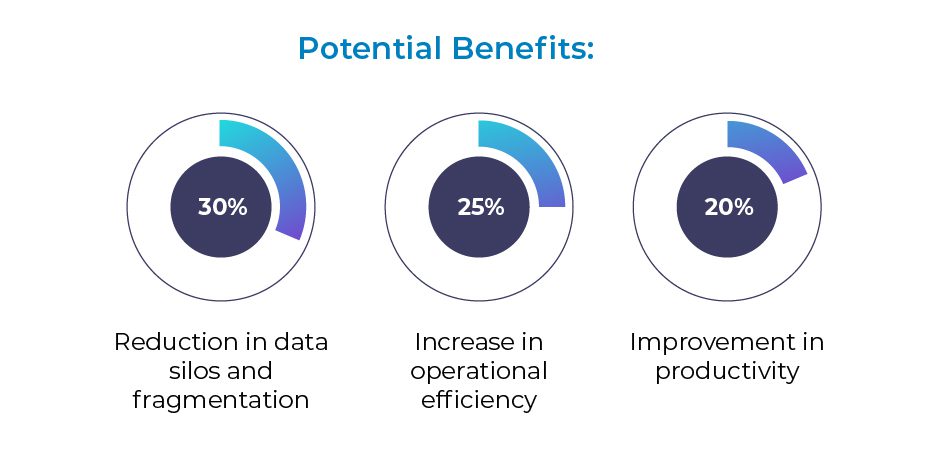
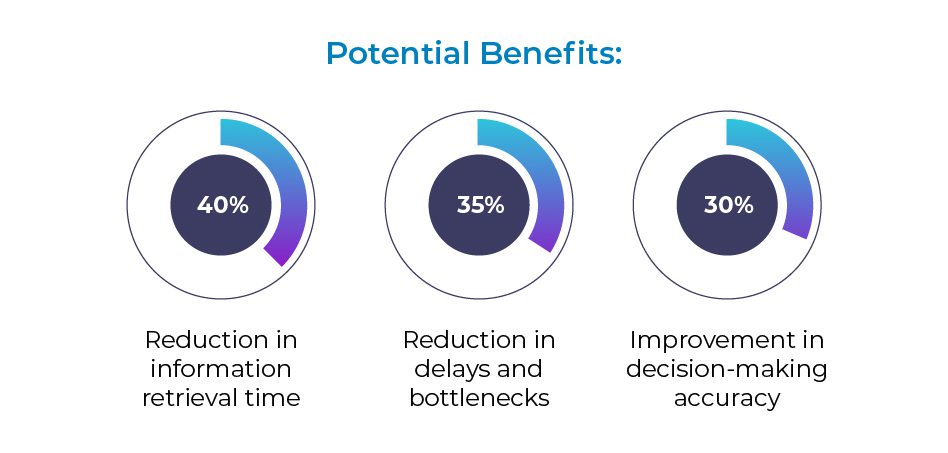
2. Enhanced Data Accessibility and Visibility
By leveraging a unified data management platform, organizations gain enhanced accessibility and visibility into critical data. This empowers stakeholders at all levels to access relevant information in real-time. Operators can monitor production processes, managers can analyze performance metrics, and executives can gain comprehensive insights into overall operations. Such transparency fosters collaboration and informed decision-making across the smart factory ecosystem.
3. Advanced Analytics and Predictive Insights
A unified data management platform serves as a foundation for advanced analytics and predictive modeling within smart factories. By leveraging integrated data, organizations can employ machine learning algorithms and AI-driven analytics to uncover patterns, identify anomalies, and generate predictive insights. This enables proactive maintenance, optimized production planning, and improved quality control, leading to enhanced efficiency and reduced downtime.
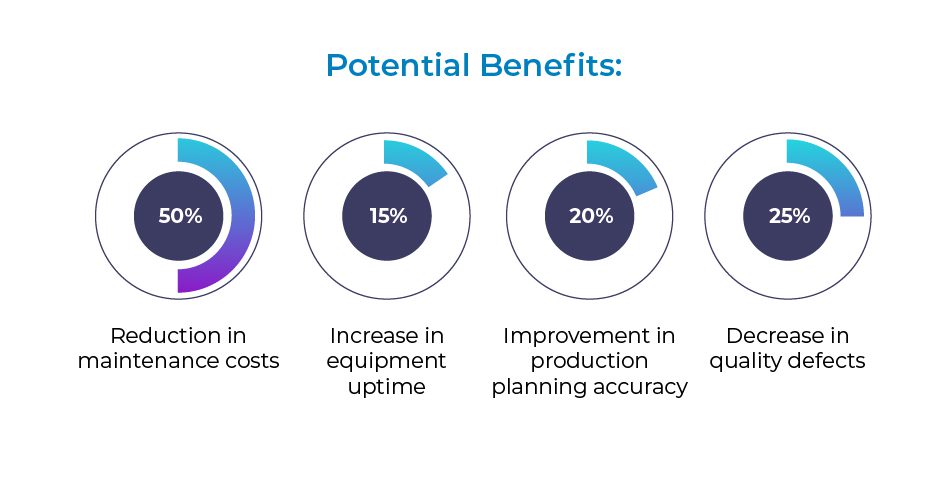
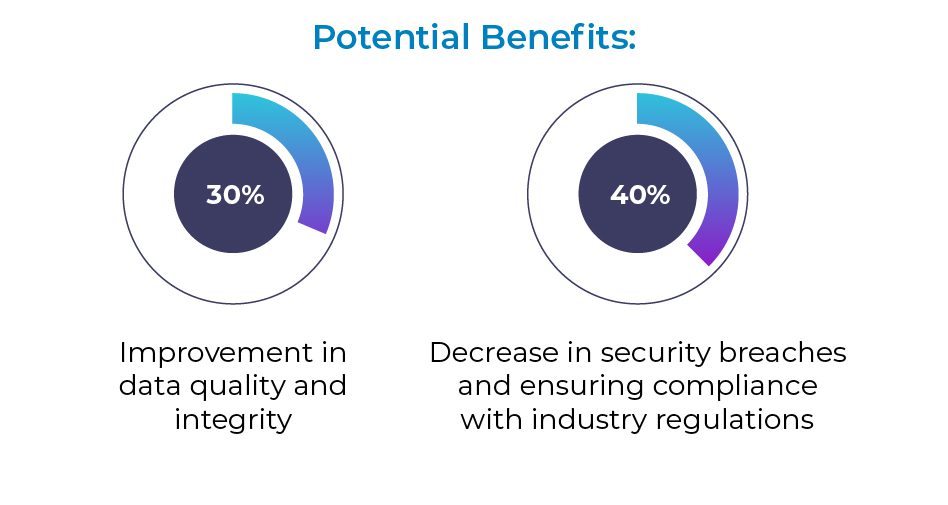
4. Data Governance and Security
Implementing a unified data management platform ensures robust data governance and security. Organizations can establish standardized data policies, access controls, and data privacy measures with centralized control. This safeguards sensitive information, mitigates risks, and ensures compliance with regulatory requirements. A secure data management foundation is crucial for maintaining trust and reliability within the smart factory environment.
5. Scalability and Future-Readiness
A unified data management platform provide scalability and future readiness for smart factories. As the manufacturing ecosystem evolves, the platform can accommodate increasing data volumes, additional data sources, and emerging technologies. This flexibility enables organizations to adapt and scale their smart factory operations, embracing new innovations and ensuring long-term success.
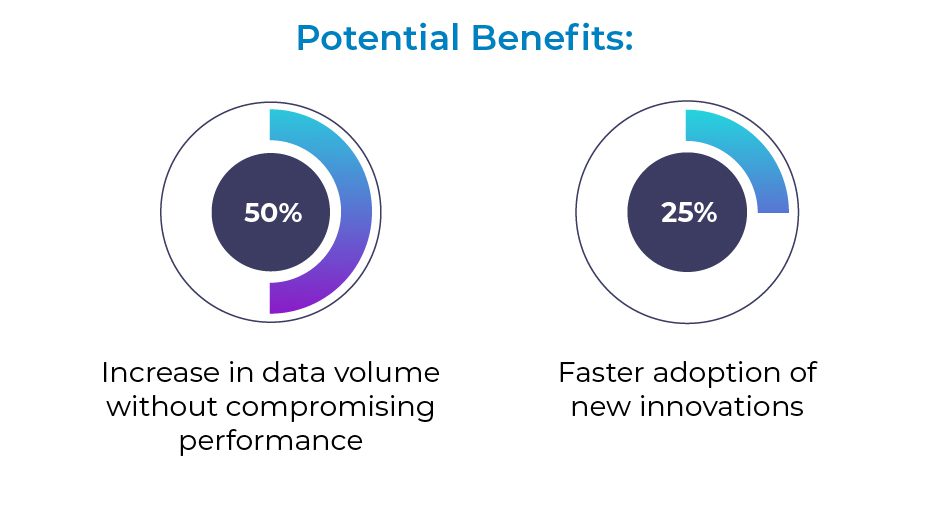
The Data Dynamics Advantage
In a world hurtling towards the transformative era of Industry 4.0, the manufacturing landscape is undergoing a seismic shift, driven by the rise of smart factories and the staggering amount of data they generate daily. Leading this charge is Data Dynamics, an empowering force that guides manufacturers through the intricate realm of data management, facilitating a seamless adoption of Smart Factories. With its comprehensive suite of solutions, Data Dynamics addresses crucial areas such as infrastructure optimization, risk and compliance, and digitization through cloud migration. At the heart of their mission lies the Unified Unstructured Data Management Platform, a game-changing innovation that enables organizations to harness the true power of unstructured data. This revolutionary platform encompasses four powerful modules – Data Analytics, Mobility, Security, and Compliance – and has already garnered immense success, serving over 300 organizations, including 28 Fortune 100 and 5 Fortune 500 manufacturing enterprises. Let’s delve into how Data Dynamics empowers manufacturers across these pivotal areas:
- Unlocking Data’s Potential: With our advanced metadata analytics capabilities, Data Dynamics enables organizations to gain invaluable insights into their data attributes. This knowledge equips manufacturers with the ability to make informed decisions on storage, retention, and archiving. By optimizing data infrastructure, relevant information becomes readily accessible for Smart Factory operations, enhancing efficiency while reducing storage costs.
- Navigating Risk and Compliance: The complex world of risk and compliance can be daunting for manufacturers. But with Data Dynamics as your ally, you’ll have the confidence to tackle any challenge. Our sophisticated content analytics and audit functionalities help organizations analyze data content, identify sensitive information, and ensure adherence to industry regulations. By proactively safeguarding against data breaches and maintaining data integrity, manufacturers minimize legal and financial risks. With an indispensable audit trail, compliance efforts during audits and investigations become streamlined and efficient.
- Accelerating Digitization: Embracing the digital revolution is no longer an option; it’s a necessity. Data Dynamics understands this, and we’re here to facilitate your journey. Leveraging our expertise in cloud technology, we make seamless cloud migration a reality. Manufacturers can effortlessly transition their on-premises data and applications to cloud-based environments, unlocking unparalleled scalability, agility, and cost savings. Our migration solutions ensure minimal disruption to ongoing operations while enabling efficient data transfer, automated workload migration, and seamless integration with diverse cloud platforms. With Data Dynamics, manufacturers can embrace advanced analytics, machine learning, and the transformative capabilities offered by Smart Factories.
Click to read
The Data Dynamics platform is the ultimate one-stop solution that empowers manufacturers to fully leverage unstructured data and gain a competitive edge in the market by implementing the latest tech revolutions like the smart factory. To learn more about Data Dynamics, please visit – www.datadynamicsinc.com or contact us at solutions@datdyn.com I (713)-491-4298.